Client story
Client: Takenaka | Industry: Construction, Automation
Breakthrough construction automation for Takenaka
Japan is a seismically active country with some of the most rigorous building regulations on earth. Collaborating with leading construction company Takenaka Group, CC has created a ground-breaking robotic guidance system for installing steel plates that are crucial for earthquake resistance. The innovation has transformed construction site safety and efficiency – and offers the promise of valuable new revenue streams.
Innovation that improved Takenaka’s operations…
Time saving of up to 50%
Workforce cost saving of 25%
Improved worker safety
Our multidisciplinary innovation team delivered the breakthrough by combining its deep tech expertise in robotics, autonomy, sensor fusion and edge AI with an off-the-shelf sensing solution. Against a backdrop of regulatory challenges and shortage of skilled labour, the system has almost halved steel plate installation times, reduced workforce costs by a quarter, and significantly improved levels of safety within the working environment.
As well as increasingly rigorous earthquake related regulation, the construction industry in Japan is facing increasing costs in both labour and materials. This trend is exacerbated by a shrinking labour market, caused by an aging population and a reluctance among younger workers to take manual jobs. Legislation in early 2024 put further limits working hours – and so increased the need for more efficient working practices. Our breakthrough in semi-autonomous robotics is certainly timely.
Takenaka Group is one of the top five general construction companies in Japan. Its large-scale civil engineering focus includes the construction of bridges, flyovers and tunnels – among a range of important public and private infrastructure projects. It faces significant operational challenges in the availability of skilled labour, ensuring safety and addressing increasing costs.
One activity that is especially labour intensive and dangerous for staff is the installation of steel plates for seismic reinforcement of existing infrastructure. The conventional approach involves the use of workers and supporting equipment to manoeuvre large steel plates from storage to the mounting position on the support pillars that are being reinforced.
The heavy steel plates, ranging from 100 to 300kg, need to be positioned with tolerances as low as 6mm to align plate holes to bolts within each column. The work has a high risk of injury and demands significant effort from experienced staff – a requirement that can restrict productivity when the right people are not immediately available.
Fit for purpose semi-autonomous robotics
Autonomous technology is advancing rapidly. But using the latest technology just because it exists is not the right approach. Considering what technology is best to achieve the business goal is key to successful innovation. That’s particularly true in this digital transformation space – which is known as construction DX.
Takenaka realised that a fully autonomous solution was not the right direction. There are many, varied situations that require such steel plates, so having a system that could adapt to all possibilities would be unnecessarily complicated to develop and to build. That’s why the Takenaka team came to us with a brief to develop a system that could be retrofitted to existing lifting construction equipment.
Takenaka had already identified a lifting and manipulation device that could position the steel plates with input from an operator. But getting the positioning right was hard and did not result in a workforce reduction or speed benefits. They needed a guidance system that was able to:
- Define the best route to move the plate towards its mounting position (all within a very limited workspace)
- Guide the construction worker to properly align and adjust the manipulator machine so that plate holes move accurately towards the mounting bolts
By combining this existing lifting device with our new sensing and control guidance, Takenaka would be creating a bespoke semi-autonomous robotics system.
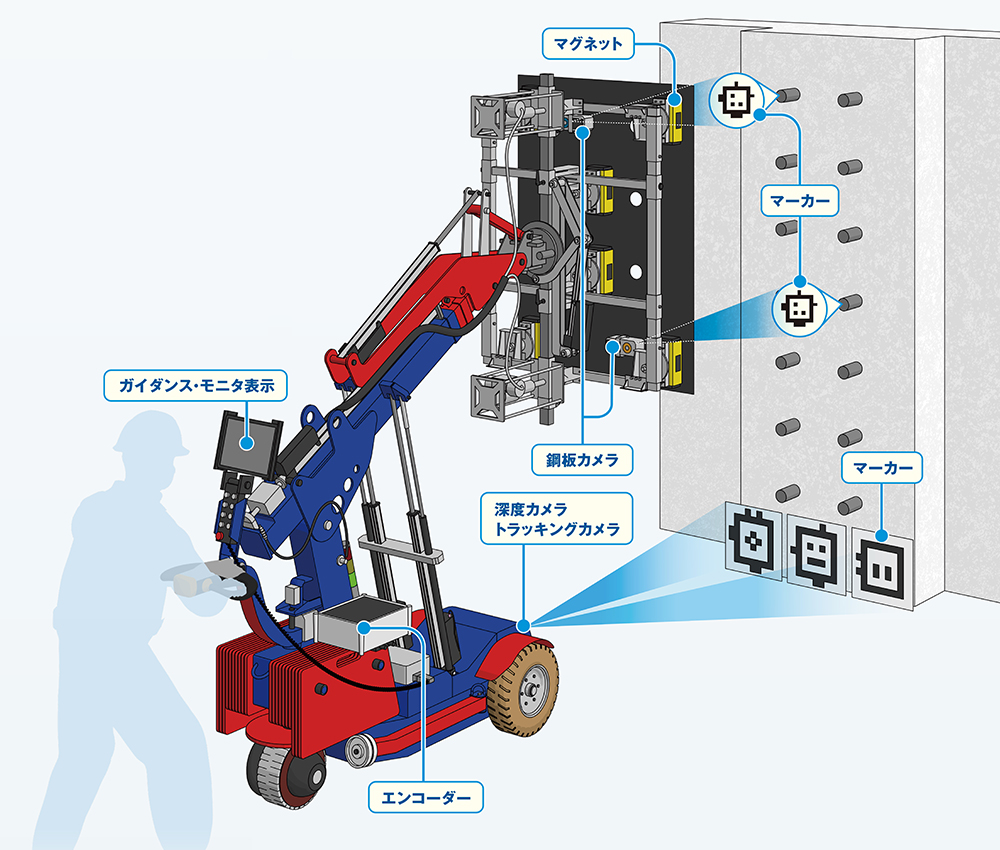
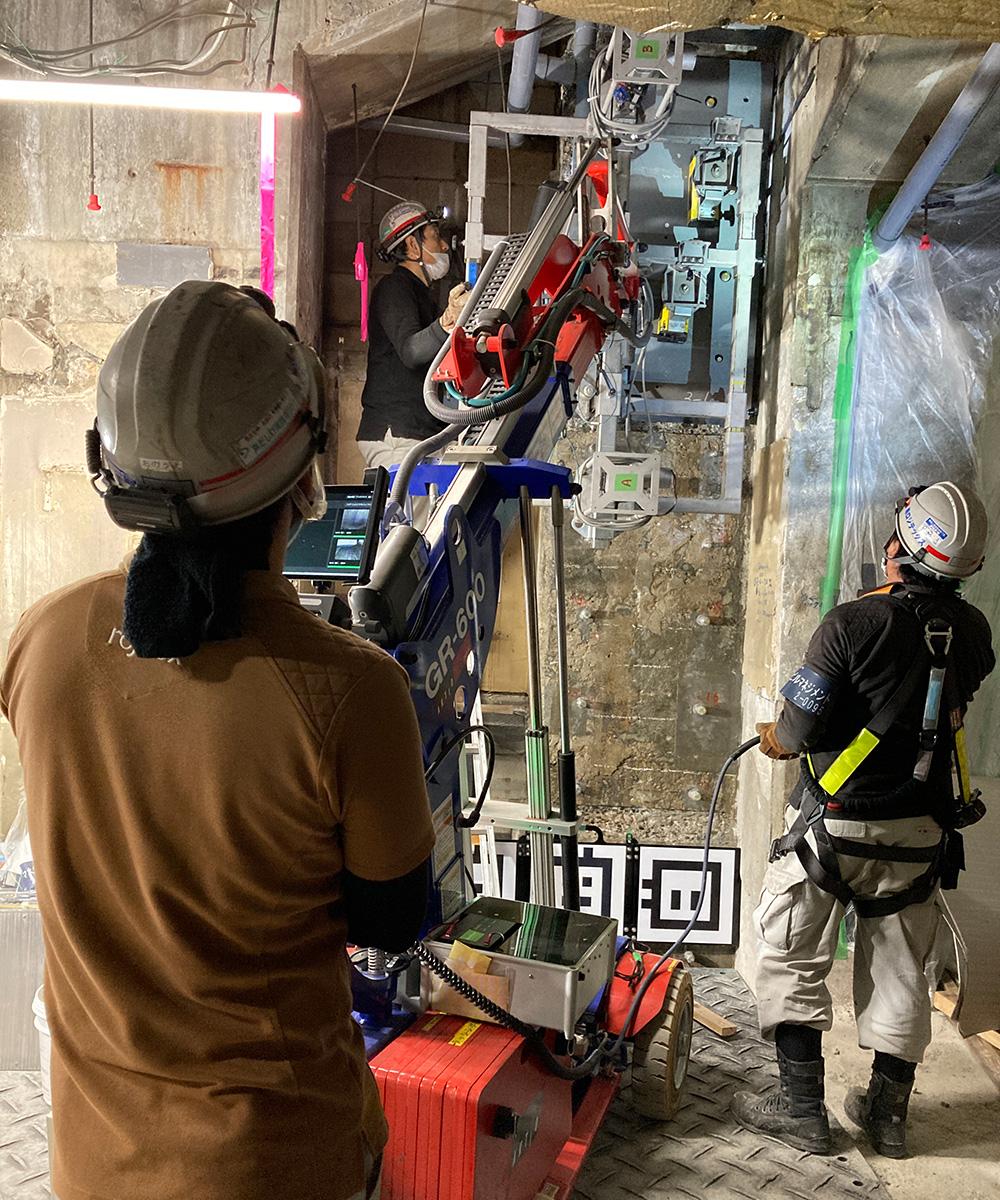
The importance of UX in construction DX
The CC team drew on a range of technologies and disciplines to drive the project towards success. Among the expertise required was a knowledge of sensing, detection and tracking algorithms; robotics and kinematics; complex multi-component software frameworks; custom hardware and electronics; and deployment on edge computing hardware.
But just as important was the need to include user experience (UX) considerations in the technology development to ensure that it was fit for purpose – and would be welcomed and readily adopted by operators and managers alike.
CC was on hand for the full lifecycle of the project, from inception to proof-of concept, prototype development and on-site handover. Our service spanned:
- Research into and understanding of the needs of both the business and its workers
- Translation of these findings into system requirements
- Identification of potential technology combinations
- Filtering and testing/assessment of the above
- Architecture creation
- Demonstration and prototype build to understand real-world performance
- Design evolution
- Creation of mature prototype for on-site use and testing
- Performance monitoring to support longer-term system development as we hand over design authority to Takenaka and their manufacturing partners
Immediate impact, with growth potential
The system uses a unique combination of sensing technologies and bespoke algorithms to guide the operators in positioning the lifting equipment, and then guide the manipulation of the plates onto their bolts. This easy-to-set-up and easy-to-use system does the job of one or two workers who would otherwise have to watch and provide instructions to the operator of the lifting equipment.
The system has received enthusiastic feedback from workers on the ground. They benefit from a much-reduced manual burden, as well as an increase to efficiency and levels of safety.
As for what comes next, Takenaka and CC are considering further ways to apply the technology innovation of construction DX into civil engineering work. In addition to scaling up the use of the system, Takenaka is exploring similar applications for the same core technology, and we continue to discuss other areas of the business where technology innovation can have a significant impact.
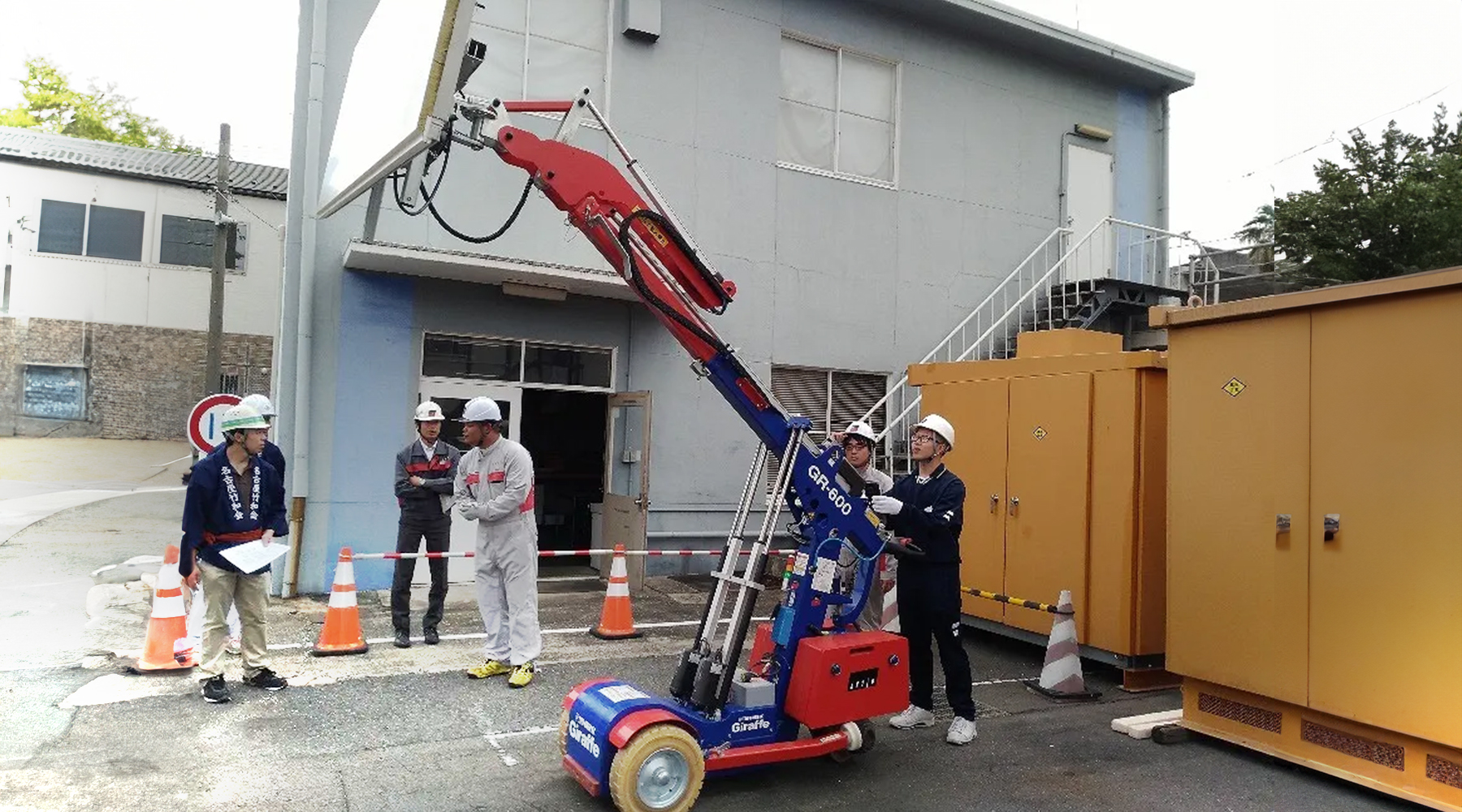
“CCs’ expertise and commitment augmented our in-house skills and enabled us to overcome challenges that we couldn’t have solved on our own. We collaborated perfectly as a team, even though project members from CC were sitting in different parts of the world.”